Automotive
In automobile manufacturing, the coating production line plays a pivotal role. The process starts with the pre-treatment of the car body. Through degreasing, phosphating and other processes, the oil and impurities on the surface of the car body are thoroughly removed to create an ideal base for the subsequent coating adhesion. Then, electrophoretic coating comes on stage. The car body is immersed in the electrophoretic paint tank, and the electric field is used to make the paint adhere evenly, ensuring that the hidden parts such as the inner cavity and gaps of the car body can be perfectly covered, greatly enhancing the anti-rust ability.
Then comes the mid-coat stage, where the spray gun sprays finely to fill in the minor flaws in the electrophoretic layer, improve the flatness of the paint surface, and provide good support for the topcoat. The topcoat spraying stage is a feast of color and craftsmanship. The robotic arm controls the spray gun to accurately control the paint flow, atomization degree, and spraying trajectory. Whether it is a fashionable solid color, a cool metallic color, or a gorgeous pearlescent color, it can be perfectly presented, making the car look dazzling while resisting external erosion such as ultraviolet rays and acid rain.
Finally, after drying and curing, the coating is firmly locked in, which not only gives the car a long-lasting and bright appearance, but also provides solid protection for the car body during years or even decades of use, safeguarding the structural integrity of the car, which is an indispensable key link in car quality assurance.
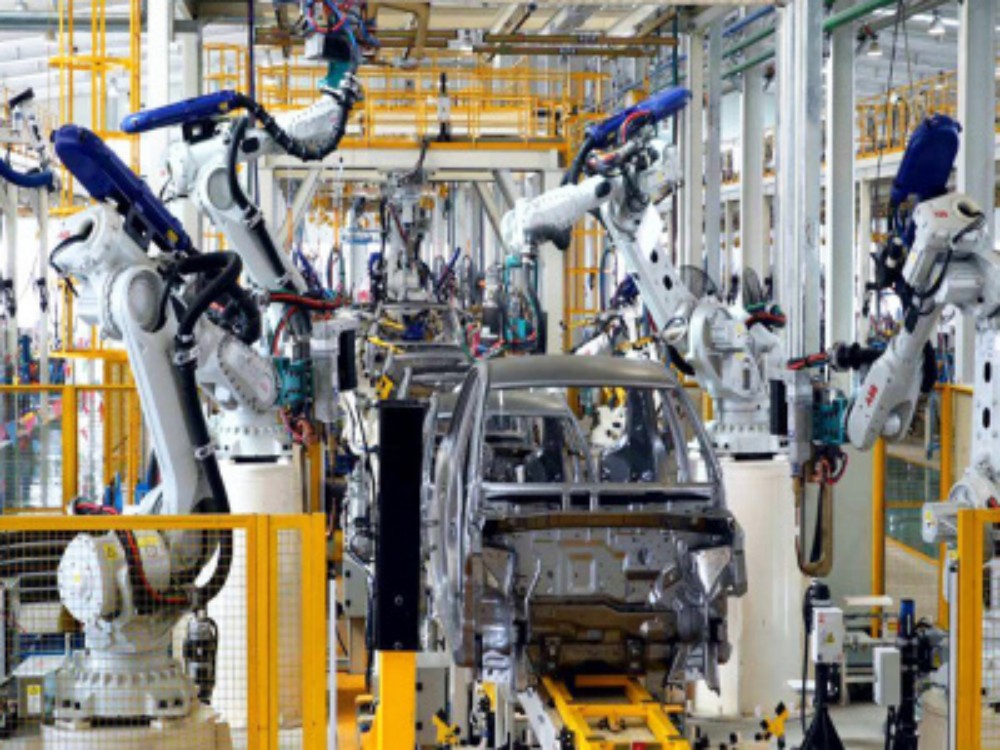
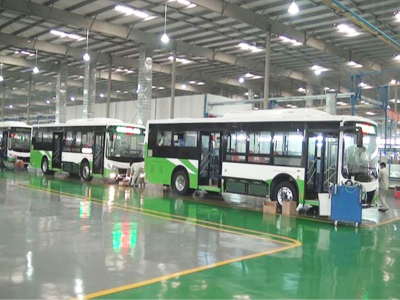
Commercial Vehicles & Semis
In the field of Commercial Vehicles & Semis, various production lines work together to create a solid steel behemoth. The painting production line starts the journey of protection and beautification. The pre-treatment deeply cleans the body, and the electrophoresis, mid-coat and topcoat are added layer by layer to cover the vehicle with a "battle suit" that can resist sand and gravel impact and has super weather resistance, ensuring that it will remain new over long journeys and complex road conditions. The welding production line is the "welding master" of steel. It uses arc welding, spot welding and other processes to accurately connect key components such as beams and frames, build a stable structure that can carry heavy objects and ensure driving safety. The powder spraying production line focuses on the chassis, wheels and other parts, sprays powder evenly, forms a dense protective layer, effectively resists road salt and mud erosion, and extends the service life of components. The final assembly production line is like a precise "commander-in-chief", assembling engines, gearboxes, axles and various interior parts in an orderly manner, allowing commercial vehicles and semi-trailers to drive out from the end of the production line one after another, rushing to various battlefields such as logistics transportation and engineering construction, and promoting the vigorous development of the industry.
Industrial Manufacturing
In the vast world of Industrial Manufacturing, these four production lines are the backbone. The coating production line is like a magical painter. After carefully completing the pre-treatment process for large-scale mechanical equipment, it uses professional spraying technology to apply protective paint, so that it can operate normally in high temperature, high humidity or corrosive environments, while giving the equipment a beautiful appearance and enhancing brand recognition. The welding production line is the embodiment of the steel elf. With exquisite skills such as arc welding and laser welding, it accurately welds various metal plates and pipes to create a solid core for industrial robots, heavy machine tools, etc., to ensure high-intensity operation needs. The powder spraying production line is like a protective messenger, focusing on the transmission parts and supporting structures of the machinery, spraying powder evenly, with its excellent insulation and wear resistance, helping the equipment to cope with frequent friction and electrical interference, and extending its service life. The final assembly production line is like a smart center. According to the precise design blueprint, it orderly combines engines, control systems, robotic arms and other components, allowing advanced industrial manufacturing equipment to be successfully born, and devotes itself to cutting-edge fields such as intelligent manufacturing and energy mining, injecting surging power into industrial progress.
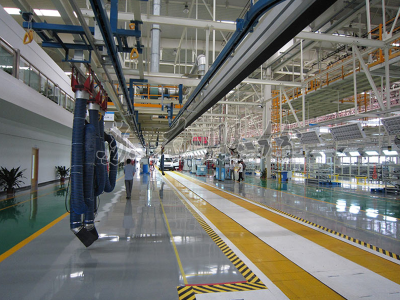

Large Parts & Equipment
In the field of Large Parts & Equipment, these four production lines each demonstrate their unique capabilities. The coating production line is like an artistic master. Facing giant steel structures, large machinery casings, etc., it carefully performs pre-treatment such as degreasing and rust removal, and uses high-pressure airless spraying and other processes to apply high-temperature resistant and anti-corrosion protective paint, so that it can withstand harsh working conditions for many years and greatly improves the appearance texture. The welding production line is like a steel craftsman. It uses a variety of welding methods to accurately splice ultra-thick steel plates and large castings, like building a solid foundation for large bridge components and mining machinery bodies to ensure stable load-bearing. The powder spraying production line is like a guardian. It evenly sprays powder on key connection points and easily worn parts of large equipment. With its excellent impact resistance and anti-oxidation properties, it allows the parts to prolong their life under frequent operation, wind and sun. The final assembly line is like a precision navigator. According to rigorous planning, it methodically integrates the power system, complex control components, etc., enabling large and sophisticated equipment to be successfully rolled off the production line and rush to ports for loading and unloading and large-scale construction sites, pushing the industry forward in great strides.