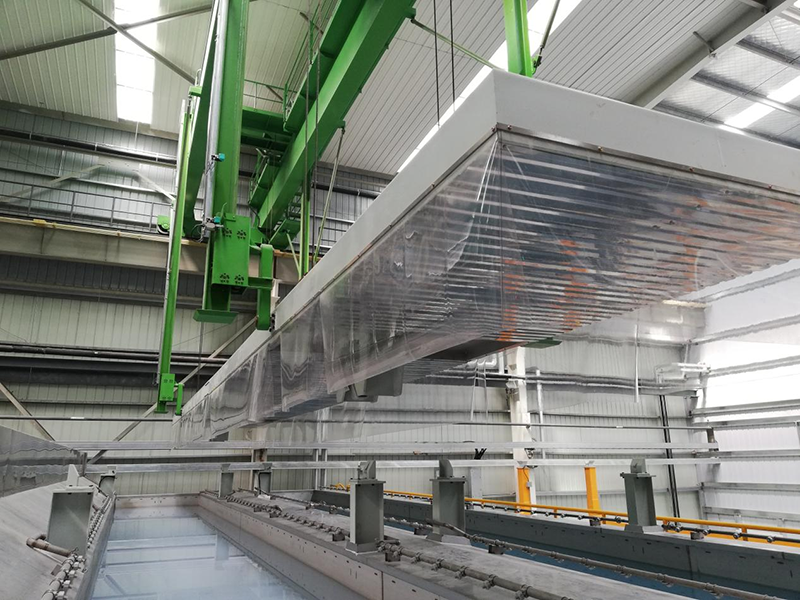
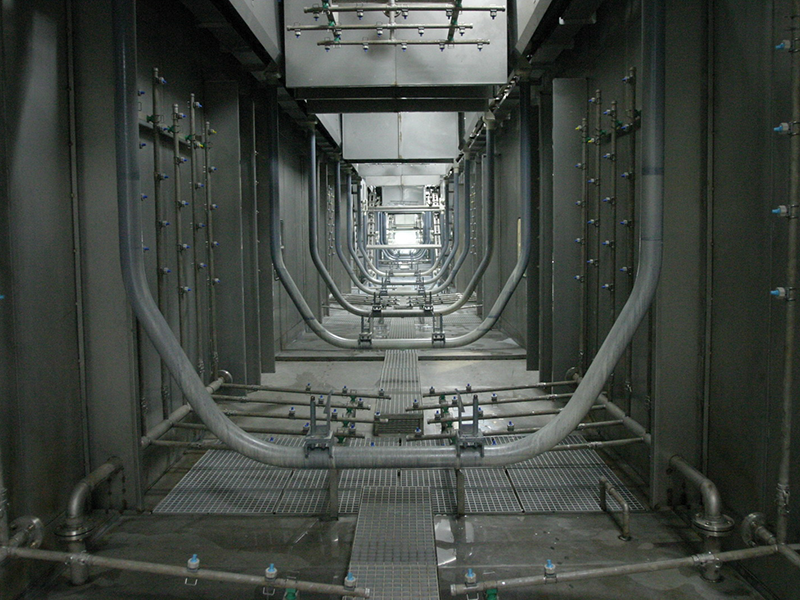
Electrophoretic coating is the same as other coating methods. The coated parts need to be surface treated before coating. Surface treatment is an important work that needs to be done before coating. Different coating methods, different materials and their surface conditions, so The required surface treatment processes and methods are not the same. Not only do different surface treatment processes and treatment quality seriously affect the coating quality, but also the surface treatment cost has a greater impact. Therefore, when we carry out technical design, we must The installation method, the material and surface state of the coated parts, and the surface treatment process and method with strong pertinence, good treatment effect and relatively low cost should be selected as much as possible.
Why does electrophoresis have a pretreatment process?
In the pretreatment process of electrophoresis, there are mutual cooperation of degreasing, rust removal, phosphating, surface adjustment and other processes. It can be said that pretreatment is indispensable in electrophoretic coating, which is related to the stability of the electrophoretic paint bath after electrophoresis and the quality of the coating film on the surface of the workpiece.
In order to obtain the durability and corrosion resistance of the coating film of the electrophoretic workpiece, phosphating treatment is used as the pretreatment of the coating. Phosphating treatment (also known as phosphate chemical treatment) is a (phosphating film) technology that uses the dissociation (equilibrium) reaction of phosphoric acid to precipitate insoluble phosphate metal salts on the surface of cleaned (degreased) metal substrates. The function of the phosphating film is to improve the adhesion and corrosion resistance of the coating film (electrophoretic coating) applied on it.
Regarding the adhesion, the crystals of the obtained phosphide film are slightly dissolved into the metal surface, and the adhesion of the crystals is good. In addition, the surface area is increased due to the surface unevenness of numerous crystals, and the adhesion of the coating film is improved. Then, with the improvement of the adhesion of the coating film, the intrusion of corrosion-producing substances is prevented, and the corrosion resistance is improved (especially the corrosion expansion under the paint film can be prevented).
The coating will blister and rust in a short period of time without phosphating. The water and air passing through the coating film reach the surface of the workpiece to form red rust and swell the paint film. The water and air passing through the coating film reach the galvanized steel sheet to form white rust, which also reacts with the coating film to form metal soap. A few times larger, so that the coating film is more vigorously puffed up. Phosphating film is an insoluble film formed on the metal surface by chemical reaction. Due to its good adhesion (physical) and chemical stability, it is treated as a durable anti-rust coating substrate.
In order to obtain an excellent and stable phosphating film and ensure its adhesion and corrosion resistance, the management of pretreatment is very important. At the same time, it is necessary to have a good understanding of the basic reaction mechanism and elements of phosphating treatment.
Post time: Jul-08-2022